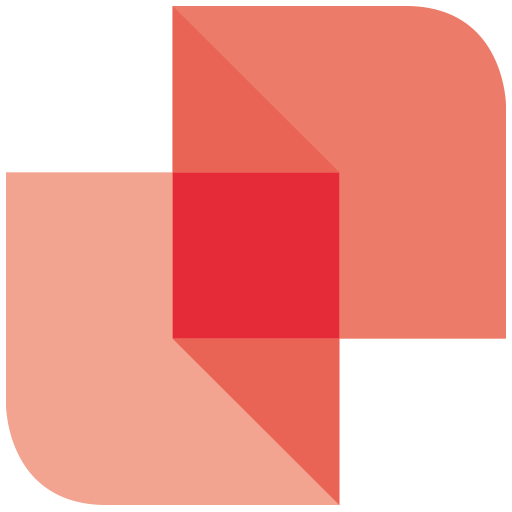
Quando la cabina fa acqua
Sempre più, oggigiorno, le postazioni di lavoro e le attrezzature impiegate nello svolgimento delle diverse mansioni sono soggette a continue migliorie. E non solo per lavori prettamente manuali. Ricordiamo ad esempio che per un funzionario commerciale, che deve macinare chilometri, le macchine fornite dall’azienda sono sempre più confortevoli (volante riscaldato, sedili che fanno i massaggi…) […]