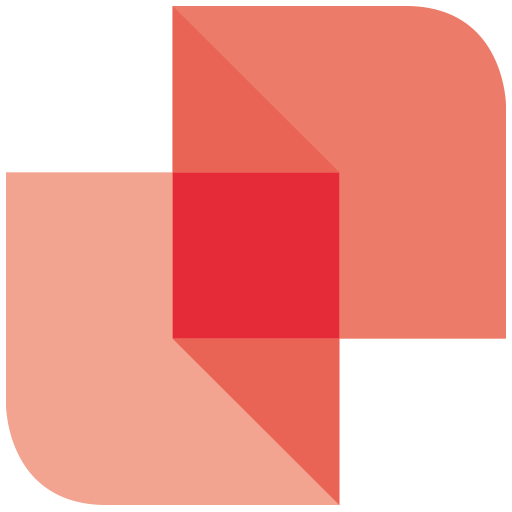
Verniciatura a polvere
Diversamente dai processi di rivestimento con vernici liquide (ad acqua o a solventi), la verniciatura a polvere si effettua a secco, utilizzando come materia prima differenti tipi di polveri colorate a base di resine sintetiche. Il veicolo di trasporto è in questo caso l’aria, che viene miscelata alla polvere all’interno di una apposita pistola elettrostatica. […]