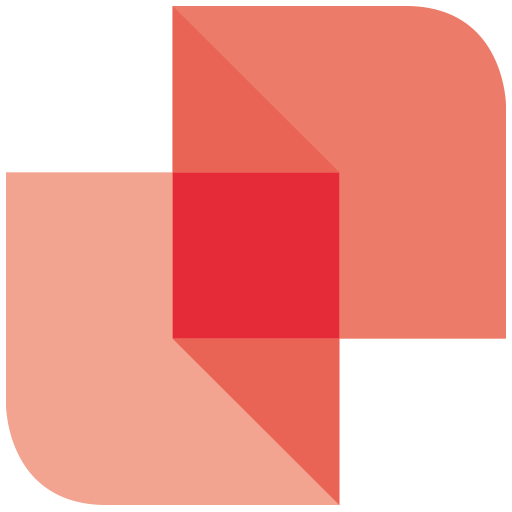
ASHRAE 52 – Parte 2
LA ASHRAE 52.2-1999 Successivamente, nell’ambito di alcuni contaminanti specifici, ASHRAE ha riconosciuto la necessità di definire uno Standard in grado di fornire agli utilizzatori uno strumento di valutazione dei filtri basato sull’abilità del filtro di rimuovere uno specifico contaminante, in funzione delle dimensioni delle sue particelle. Inoltre, anche relativamente alle particelle “respirabili” (particelle che posso […]