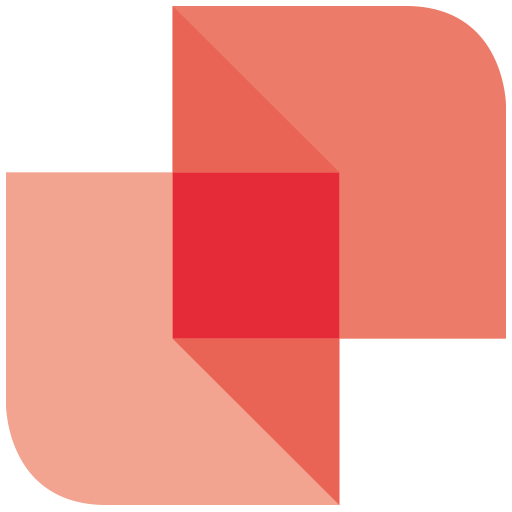
La riduzione dell’overspray
Per “overspray” si intende quella parte di vernice spruzzata che non si deposita sulla superficie da verniciare. Per sua natura, l’overspray non porta alcun beneficio al processo di rivestimento. Al contrario, risulta essere un onere in quanto incrementa la quantità di materiale che deve essere smaltito, incrementa il carico dei filtri, imbratta la cabina ed […]