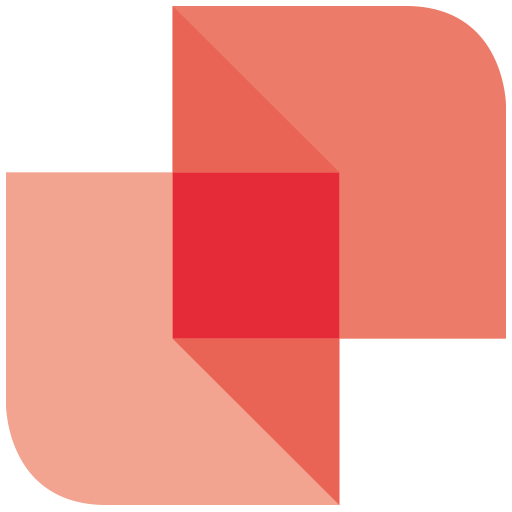
La Ventilazione Meccanica Controllata
Negli ultimi anni è cresciuta l’esigenza di migliorare il livello di vita e degli standard qualitativi e di comfort degli edifici, unitamente a quella di contenere il più possibile le dispersioni termiche e quindi ridurre il consumo energetico. Assistiamo così, sia nelle nuove costruzioni che nella ristrutturazione degli edifici esistenti, all’utilizzo di tecniche e tecnologie […]