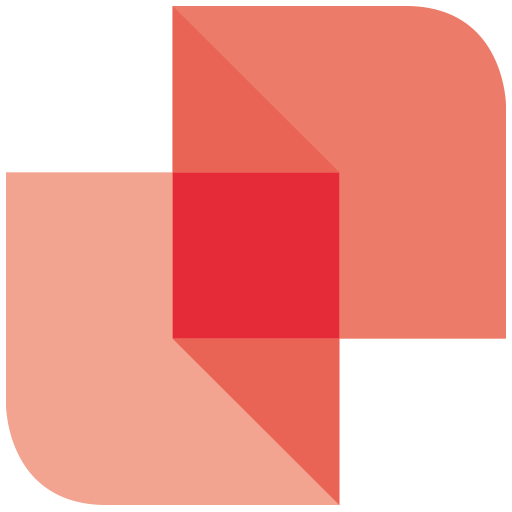
La norma ISO 16890
A cosa serve la norma ISO 16890 La norma ISO 16890 è stata studiata con l’intento di rendere più intelligibile per l’utilizzatore finale la classificazione dei filtri per ventilazione più chiara per i progettisti la prescrizione delle sezioni filtranti. La ISO 16890 unifica e tende a sostituire lo standard europeo EN779:2012 e quello americano ASHRAE […]