La qualità delle lavorazioni e la produttività, la sicurezza e la salute sul luogo di lavoro, l’aria pulita richiedono tutti un sistema di ventilazione forzata, che fornisca un adeguato e costante flusso di aria mentre la cabina è in funzione; esso deve mantenere la concentrazione di vapori di VOC al di sotto del livello minimo di infiammabilità (LEL), deve aiutare a ridurre la necessità di lavorare di nuovo pezzi già processati, deve provvedere all’immediata cattura dell’overspray, indirizzandolo ad un appropriato sistema di abbattimento, deve evitare che si formino zone di accumulo di vapori o polveri in prossimità dell’operatore.
Non tutti i sistemi a ventilazione forzata sono in grado di fornire le prestazioni richieste: può capitare, ad esempio, che della polvere si ridepositi sulle superfici appena verniciate (spesso i verniciatori che hanno esperienza di ciò, ne imputano la causa alla mancata efficienza dei filtri per particolato ma, talvolta, nonostante la sostituzione degli stessi, il fenomeno non scompare); oppure che si formino concentrazioni pericolose di overspray e VOC causando condizioni di non sicurezza sanitaria per gli operatori che le respirano; oppure che si riduca la portata d’aria di aspirazione, man mano che i filtri si caricano di overspray, con conseguente mancato rispetto dei limiti di velocità minima dell’aria in cabina previsti dalla normativa vigente.
Per inciso, questi problemi possono sorgere indifferentemente sia in cabine a flusso verticale che a flusso trasversale, sia in cabine a secco che in cabine ad acqua.
Linee di flusso aerodinamiche
La chiave per una continua ed efficiente operatività della cabina, sia essa grande o piccola, è la progettazione dei flussi d’aria e l’installazione dei più efficienti dispositivi per il controllo e l’abbattimento delle polveri, sia sotto forma di particolato che di overspray (per una panoramica dei filtri utilizzabili si veda questa pagina).
In linea generale, la situazione ottimale è quella tale per cui le linee di flusso si mantengono uniformi per l’intera lunghezza dell’apertura del condotto di aspirazione; con questa configurazione (vedi figura – fonte Airflow Patterns in Spray Booths, PCI Magazine, 2005), si elimina la formazione di vortici e di “zone morte” (sacche di aria ferma), con il triplice scopo di proteggere le superfici verniciate, l’operatore e la sicurezza dell’ambiente .
Non dimentichiamo infatti che esiste una specifica normativa tecnica
[EN 12215 (2009): Impianti di verniciatura – Cabine di verniciatura per l’applicazione di prodotti vernicianti liquidi – Requisiti di sicurezza;
EN 12981 (2009): Impianti di verniciatura – Cabine per l’applicazione di prodotti vernicianti in polvere – Requisiti di sicurezza]
la quale impone che tutte le cabine debbano essere dotate di un sistema di ventilazione forzata in grado di rimuovere adeguatamente i vapori infiammabili, le nebbie, il particolato e confinarli in luogo sicuro.
Le tecniche per raggiungere questo obbiettivo sono diverse, ma non sempre risultano efficienti.
Vediamo nel dettaglio alcune possibili criticità.
Una tecnica utilizzata è quella di fare in modo che l’aria prelevata dall’esterno ed immessa in cabina, spinga l’overspray e i vapori di VOC verso la griglia di aspirazione. Se il flusso d’aria in ingresso e quello in uscita non sono bilanciati, si vengono inevitabilmente a creare vortici e turbolenze che diminuiscono le prestazioni globali della cabina: i vortici sono infatti causa invisibile di rideposizione dell’overspray sulle superfici verniciate.
Anche la presenza dei filtri non garantisce che si possa ottenere un flusso d’aria uniforme, poiché l’aria segue naturalmente i percorsi dove incontra la minore resistenza.
Se il sistema non è bilanciato, i filtri possono catturare il particolato in maniera non uniforme e si possono verificare situazioni come quelle illustrate in sequenza nelle seguenti figure (fonte Airflow Patterns in Spray Booths, PCI Magazine, 2005), dove l’intasamento dei filtri (clogged filters) procede per settori e genera linee di flusso non ottimali.
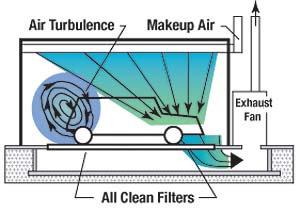
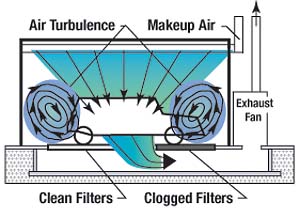
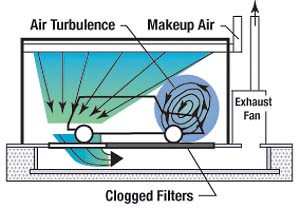
Situazioni simili si possono verificare in qualsiasi tipo di cabina, non solo quelle con filtri a secco.
Alcune cabine ad acqua sono progettate per creare un velo d’acqua uniforme avente lo scopo di catturare l’overspray trasportato dall’aria di aspirazione; se la portata d’acqua che forma il velo e la portata dell’aria esausta non sono calibrate correttamente, si possono creare delle “smagliature” nel velo all’interno delle quali l’overspray passa liberamente senza essere abbattuto (depositandosi successivamente nei condotti di aspirazione, sul ventilatore, ecc.), rendendo inefficiente l’intero sistema di captazione.
In altre cabine, invece, sono installati dei sistemi per miscelare acqua nebulizzata con l’aria contaminata. Uno dei problemi che si possono presentare è dovuto al tipo di ugelli utilizzati che, se non accuratamente selezionati anche in funzione del tipo di vernice usata, possono intasarsi con conseguente perdita di efficienza, oppure non essere in grado di fornire una sufficiente superficie di cattura, lasciando che il particolato riesca a bypassare le gocce d’acqua.
L’utilizzatore finale, che spesso non possiede le necessarie conoscenze e competenze in materia, può rischiare di trovarsi nella condizione di acquistare una cabina che non è in grado, nel tempo, di mantenere i requisiti prestazionali e di efficienza descritti in queste brevi righe.
Chiunque può verificare visivamente la presenza di zone di ricircolo in cabine dotandosi di fumogeni con fumo ad alta persistenza.