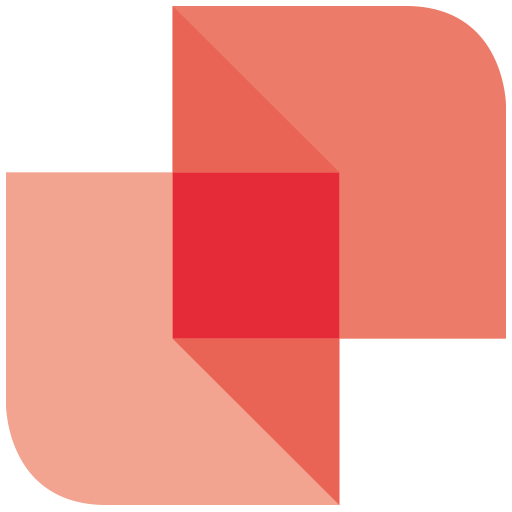
Evoluzione della Norma EN 1822
La norma europea EN 1822 “Filtri per aria ad alta efficienza (EPA, HEPA e ULPA)” si applica ai filtri per aria ad alta ed altissima efficienza e a bassissima penetrazione (EPA, HEPA e ULPA), utilizzati nel campo della ventilazione e del condizionamento dell’aria, come pure in processi tecnologici quali la tecnologia delle camere bianche o […]