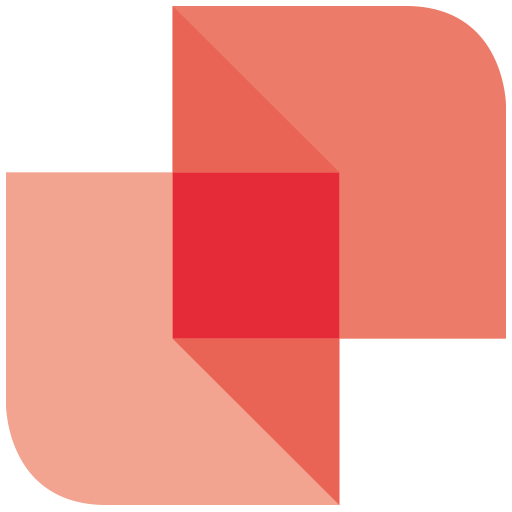
La misura dell’efficienza di filtrazione dell’overspray (parte 1)
Le emissioni industriali in atmosfera, si sa, sono uno dei problemi che il legislatore si trova ad affrontare. Se la definizione di un limite alle emissioni è opera tutto sommato semplice, non si può dire altrettanto per la fase di controllo di questo limite. Senza entrare nel merito e senza esprimere giudizi sul perché di […]